Hot cut and cold cut
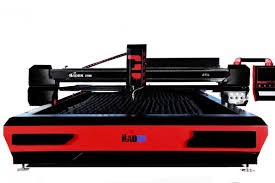
Hot cut
Hot cutting is done using a heat burner (plasma or oxy fuel) and is installed on the last axis of the multi-axis machine. The axles of the multi-axis device are powered by electric motors and are coordinated to create a path for the burner and the tube that creates the desired profile. Axis synchronization is done either mechanically, via low, levers and gears, or electronically via microprocessors and controllers.
Cold cut
Where high temperatures and combustion sources required by hot cutting are not desirable, air or hydraulic pipe cutters are used. These include a chain cut or rope cutter that has a steel and feed mechanism that rounds the tool for each round of the cycle. The tools may be designed to cut and / or prepare the cone for welding in a single or multi-purpose pass.
Due to the complexities and common specifications required in the relevant industries, it is popular in the marine industries, pipe processing, shipbuilding, pressure vessels, structural and mechanical contracting.
Some common uses for pipe cutting include:
Pipe work, marine jackets, industrial metal structures, stadiums, cranes, nozzles and plumbing stitches