History of CNC
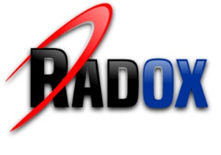
The waterjet uses water as a propellant and is mixed in an abrasive to speed up the cutting process. Waterjet cutting glass requires you to be careful when doing the job to do the job as smoothly and cleverly as possible. Even if abrasive waterjets can be supplied with the right tools, they still need care to do the cutting properly. In this article, we have done our best to teach you how to do this.
What materials can the waterjet cut?
You can use this tool in terms of cost and time because even the most complex shapes of glass can be cut without any problems. Since waterjet cutting is a non-thermal method, no area of the glass will be affected by heat during cutting, which helps maintain the structure and shape of the glass. On the other hand, because your glass will not move when cut with waterjet, there is no need to make a second cut or trim its edges.
Since the nature of the cutting current can be easily changed, waterjet can be used to cut glass in various projects. The most important advantage of waterjet cutting is its ability to cut glass and mirrors without interfering with their internal structure. This allows the glass to be cut smoothly and efficiently.
Can you cut Securite glass with a waterjet?
Even the most powerful weapons can not defeat enemies who do not surrender at the time of cutting. In this case, Securite glass is a strong enemy that refuses to surrender to cutting. You may ask why? Because these glasses are designed to break into very small pieces after damage and breakage. This means that they are currently under severe stress and any additional force applied to them will simply cause them to separate. Under these conditions even the slightest pressure from the waterjet side can easily separate them. Therefore, it is not recommended to cut Securite glasses with waterjet.
Can waterjets cut mirrors?
This is a big challenge for some cutting machines that use point laser cutting. However, there is a more economical and less risky method that uses waterjets to cut mirrors. Mirrors can be cut continuously without creating cracks or throwing glass particles.
How do mirror and glass waterjet work?
Waterjets can cut glass and mirrors effectively and smoothly without interfering with or damaging the internal structure of the glass. The cutter is connected to a high-pressure water pump and then water comes out of the nozzle and passes through the glass with a stream of water at high speed. To further assist the waterjet cutting glass, the water stream is mixed with abrasives such as garnet and aluminum oxide. Even complex cuts can be made accurately thanks to water flow control technology. Of course, make sure that the abrasives are properly incorporated into the water stream, because water without abrasives will crack and damage the glass. To do this, turn on the abrasive stream before the water flows to flow with water during the cutting process. We even suggest using a plywood board on top of your glass to absorb the force before correcting the current. This causes the abrasive material and water to be mixed with sufficient pressure before the glass waterjet cutting process begins.
Benefits of cutting with waterjet
There are several advantages to cutting glass and mirrors using the waterjet process:
• Create a smooth cut
The water flow under the pressure of the waterjet cutting machine provides an extremely smooth and controllable tool. Cutting speed control allows thin or thick glass or ceramic to cut slowly.
• An accurate cut
An all-round waterjet can cut almost any shape to a thickness of 0.1 mm. The high pressure generated by the machine's water pump provides precise accuracy for smooth cutting of holes, cuts and distortion-free details. This level of precision optimizes waterjet cutting for a variety of applications in a variety of industries - automotive, lighting, architecture, energy, marine, medical, aviation, and more.