Plasma gas
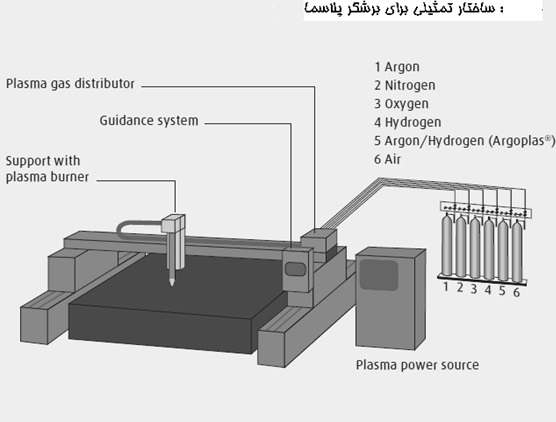
Plasma gas
Refers to all gases or gas mixtures that can be used to create a plasma and for its cutting process. The plasma arc consists of two main phases; Initial phase and cutting phase. Therefore, plasma gas is divided into two categories, starting gas and shear gas, each of which differs in gas type and volume flux.
Start gas
This gas is used to initiate the plasma arc. Responsible for facilitating the initial process or extending the life of the electrodes.
Gas cutting
This gas is required for cutting the workpiece in the plasma arc. Responsible for achieving the desired cutting quality with different materials.
Secondary gas-rotating gas-side gas
This gas encloses the plasma jet, so it cools and contracts. In this way, it improves the quality of the cutting edge and protects the nozzle when penetrating the workpiece and when cutting underwater.
Equipment for plasma cutting
Plasma power supply
The plasma power supply provides the operating voltage and shear current for the main and auxiliary arcs. The no-load voltage of the plasma cutting power supply varies between 240 and 400 volts. The power supply includes the arc pilot (auxiliary plasma arc), the combustion system (responsible for igniting the main plasma arc).
This ignition is usually done by the initial combustion of a non-conducting plasma arc using high voltage pulses. This arc is responsible for ionizing the space between the nozzle and the workpiece, thus allowing the main plasma arc to be generated.
As the arc gets longer, each leads to little or no change in shear strength.
Plasma burner nozzle and electrode
Improving plasma cutting depends heavily on the design of the plasma torch. The higher the plasma arc contraction, the higher the cutting speed and edge-cutting quality.
The key components of a plasma torch are the plasma nozzle and the electrode. Both the plasma nozzle and the component electrode have limited service life. Wrong choice or incorrect use of a nozzle or an electrode can significantly reduce their lifespan and damage the burner.
The life of the electrode is largely determined by the intensity of the cutting current, the number of combustions and the type of plasma gas used. In addition, source and gas management play a key role at the beginning and end of cutting, as well as heat loss from the electrode. Rod-shaped tungsten electrodes and needle-shaped zirconium and hafnium electrodes are used, which can be transformed into pointed or smooth electrodes. Due to the tendency to erosion, tungsten electrodes can only be used with inert plasma gases and their mixtures, as well as with low reactive and reducing plasma gases. When using pure oxygen, or plasma gases that contain oxygen, a significant increase in the life of the electrodes can be achieved by using electrodes made of zirconium or hafnium.
Gas supply source
Plasma cutting systems work with the following gases: inert, reduced reactivity, low reactivity, active and a mixture of any of these.