Plasma cutting techniques
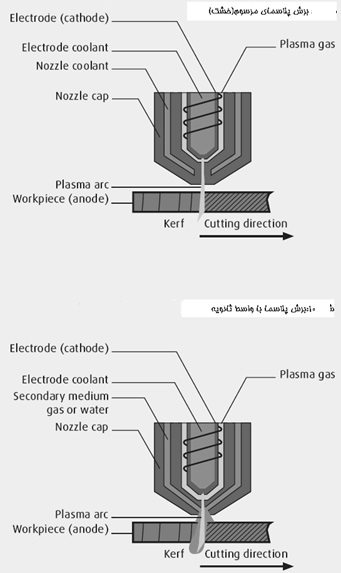
Familiarity with various plasma cutting techniques
Depending on the type of cutting material, its thickness and the output of the power supply, several types of plasma cnc cutting techniques are used.
This variety of techniques is due to the differences that mainly exist in the design of their plasma torch, corrosive system of material and (material) of their electrode material in relation to each other. Figure 8 provides an overview of the various possible options for designing a plasma torch.
Plasma cutting torches are divided into the following types based on the type of contraction, which you will get acquainted with in the following;
Conventional plasma cutting / standard plasma cutting
-Plasma cutting with secondary interface
-Plasma cutting with secondary gas
-Plasma cutting with secondary water
- Cutting water injection plasma
-Plasma incision with increased contraction
Familiarity with conventional plasma cutting
In standard plasma cutting machines, the burner is relatively simple and is designed for only one gas, the cutting gas. Commonly used cutting gases include gases such as nitrogen (N2), oxygen (O2), or a mixture of argon-hydrogen gases (Argo Plus) (Figure 9). The plasma arc, which is narrowed only by the inner diameter of the nozzle, typically produces oblique cutting surfaces (champs) in this way. In general, plasma gas moves tangentially around the electrode. Depending on the cutting speed, the burner is cooled by air or water. Conventional plasma cutting systems can be used to cut metals up to 160 mm thick.
Familiarity with plasma cutting with secondary interface
A secondary interface is embedded around the plasma arc to create a special atmosphere around it. The secondary interface can be water or a specific gas.
Familiarity with plasma cutting using secondary gas
Feeding a secondary gas around the plasma arc can cause the arc to contract more and create a special atmosphere around it; Which acts as a shield for the cutting gas and in addition, cools the cap and increases the power density, cutting quality and cutting speed. By specially fitting the protective cap, damage to the system due to short circuit and the formation of two arcs can be prevented, and thus the life of the consumable parts is increased; Thus reducing nozzle erosion). These secondary interfaces are usually called "secondary gas", "shield gas", "shielding gas", "rotating gas".Machines based on this technique are currently available for cutting metal plates to an accuracy and thickness of 75 mm.
Familiarity with water plasma cutting - shield
Another type of plasma cutting with a secondary interface is plasma cutting with water as a secondary protection; The arc is constricted by a rotating ring of compressed water, and the water forms a thin film around the arc, preventing it from evaporating immediately, which is one of the possibilities we might expect to occur. . This placement of water on the flame is like being on a perfectly uniform surface; However, in this method, 15% of the water will evaporate. The amount of water that remains (ie 85% of the remaining water) is drained from the nozzle like a conical spray and the plasma arc is broken, cooled above the workpiece surface and the formation of oxide on the machined surface is prevented. Due to this reducing effect, the hydrogen formed during the process causes the formation of a shiny and polished metal. Therefore, water-plasma cutting plasma is a preferred and practical method for cutting aluminum and alloy steels up to 50 mm thick.
Familiarity with plasma cutting with water injection
In order to create more contraction of the plasma arc, radial and uniform injection of water around its axis is used and the temperature is increased up to 30,000 degrees Celsius and the quality of the cutting surface is increased.
In this method, nitrogen gas is used as a substitute for plasma gas to apply maximum quality in metal cutting; Because nitrogen gas has a greater ability to transfer heat from the arc to the workpiece than plasma gas; In the water-injected plasma cutting method, only a small percentage of water evaporates due to the presence of an isolated vapor boundary layer between the injected water and the plasma, and the amount of water remaining leaves the nozzle at the maximum point of contraction. Cools arches and workpieces; The vapor barrier layer protects the nozzle from the extreme heat of the arc, thereby increasing the life and efficiency of the nozzle. Cooling of the workpiece with injected water and high cutting speed, cutting without distortion (curvature and distortion), Allows the formation of low protrusions (due to the small size of the heat affected area or HAZ for short) and increases the life and efficiency of the consumable parts. There are two types of plasma cutting methods based on how water is injected:
• Radial injection
(Which process is mentioned above)
• Whirlpool injection
By injecting a vortex into one of the edges - the incisions are almost vertical; While the other edge, with an angle of 5 to 10 degrees to the outside. In this method, rings of water are created around the arch, but it should be noted that its efficiency is not as good as radial injection; Because it limits the amount of arc contraction by the high rotational speed required to produce fixed rings of water; The centrifugal force created by the high rotational speed, unlike the inner hole of the nozzle, causes the water film to flatten.
✓ The advantages of the method of using plasma cutting by water injection can be: Increase cutting speed, 2. Possibility of using a gas (N2) to cut different metals, 3. Nozzle abrasion reduction 4. Improving the quality of the cut surface (the cut surface does not need to be paid after cutting and is very clean) 5. Not to mention waste under the cutting surface in most steel parts.
When using a plasma cutter with water injection, it is important that the workpiece be cut so that the side with the beveled edge is on the side of the material waste. Flat electrodes are preferred for plasma cutting. This method is used exclusively with underwater cutting machines. Using this technique, metal plates with a thickness of 3 to 75 mm can be cut.
Familiarity with plasma cutting with increased contraction
This type of cutting involves increasing the arc density by using nozzles with narrower diameter widths (narrower openings). Different companies use different methods (some of which have been patented) to contract the arch. Adjustable throttles and nozzles have generally been shown to be effective. The plasma arc created with this machine makes it possible to produce high-precision vertical cuts when cutting metal plates with a thickness between 5.0 and 25 mm (mm). Cutting plasma with increased contraction is a very selective method for situations where secondary gas is used.
In addition to the basic plasma cutting methods mentioned above, it should be noted that the press also introduces the proprietary techniques of many companies, some of which are protected by patents.
Buy a plasma cutting machine
To buy a plasma CNC machine and find out the price of a plasma CNC machine, you can refer to the Radox Group website at radoxgroup.com; Radox Industrial Group (Pajhwok Radin Sanat Danesh) is one of the largest manufacturers of CNC machines (metal cutting) in Iran and the Middle East, which has a specialized and experienced team to design and manufacture plasma cutting machines. With the most advanced technology in the world today.
All products offered by Radox Industrial Group have a 5-year warranty and 15-year 24-hour after-sales service, and due to the variety of designs, very high quality products, after-sales service, etc. are welcomed and High user satisfaction has been associated. For information on the price of plasma cutting machines, how to buy and use the special conditions for buying products with a 9% loan with a three-year payment terms, you can contact our sales experts and support team.