Introduction of various methods and methods of cutting metals
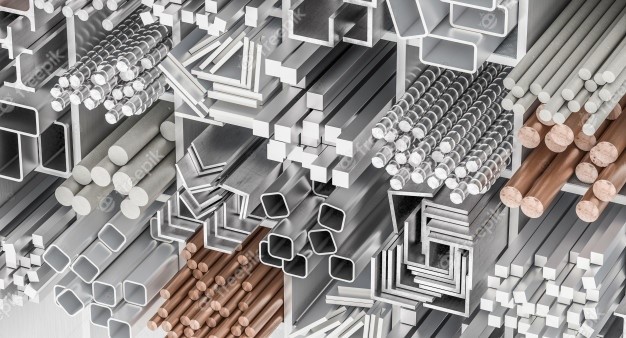
To help you decide, here are some of the most common metal cutting technologies and approaches. Along with the increasing demand for metal cutting, new cutting technologies are being developed. Which are more accurate and cost-effective. When it comes to metal processing techniques used today. The most common of these are laser cutting, plasma cutting or water jet cutting. The choice of cutting method greatly affects the overall cost of manufacturing metal positions, ie structures, as well as their quality. The question is, what is the best metal cutting technique?
Laser cutting of metals
Laser cutting of metal has been used for 25 years and the cutting technology is constantly improving. Since the early use of lasers, modern technology, especially CNC, has accurately and cost-effectively increased laser cutting, making it one of the most cost-effective cutting techniques. Depending on the power, the laser technology can cut soft metal to a thickness of 12.7 mm, a maximum stainless steel thickness of 10 mm and a maximum aluminum thickness of 5 mm. The maximum thickness of laser cut metal is 25 mm for structural and stainless steel and 15 mm for aluminum. Laser metal cutting is mostly used for cutting homogeneous structural metals, while impurities and additives greatly reduce the cutting quality. In addition to reducing quality, molten metal as an inevitable cutting product can damage the laser optical lens. Today, in practice, there is an increasing need to cut very thin materials that require additional operations during cutting. Due to the low thickness of the material, it is necessary to discharge the heat from the cutting process itself. Therefore, laser cutting is used in cutting all types of metals and the maximum thickness depending on the power of the laser. With economy and quality; The combination of laser and CNC technology allows cutting and very complex situations.
Water jet
The water jet process involves mixing water with a metal abrasive and then applying it with great force to the metal component that needs to be formed. The water jet method allows accurate metal surfaces during the fabrication process. Many professional builders rely heavily on water jet shaping and cutting because it is relatively fast and inexpensive. The water jet process also produces clean surfaces and smooth edges, known for quality materials.
Plasma
Plasma cutting has been practiced since 1960 when it was first used. In the last five years, this technique has experienced a revolutionary cut. New cutting methods have been developed that have increased the accuracy, thickness of the metal and the quality of the cut. Plasma cutting thus involves conducting negatively charged gas ions almost instantaneously at the speed of sound into the metal being cut. It should be noted that the metal has a positive charge during plasma cutting. After the plasma beam penetrates the metal, a temperature of up to 28000 Co is created. Due to the high temperature, there is a risk of corrosion, so auxiliary gas is also applied when cutting. The choice of auxiliary gas in plasma cutting depends largely on the metal being cut. For example, when cutting stainless steel, air, oxygen, or a combination of argon and hydrogen can be used, and in the case of aluminum cutting, only air can be used as an auxiliary gas. Plasma cutting is commonly used for metals with a thickness of 8 to 31.75 mm. With the advantage of high cutting speed, plasma cutting is also characterized by the development of high temperature, which can damage the material to be cut.
Which cutting technique should you choose?
When it comes to choosing the best metal cutting method, the required cutting accuracy and the properties of the cutting material must first be considered. In addition, it must be taken into account in calculating the speed or position at which the metal to be processed is to be included. Therefore, laser cutting is recommended for metals that require more complex and precise processing with high cutting accuracy and efficiency. In practice, this means that laser cutting is more economical for metal thicknesses up to 10 mm, which do not have high reflective properties as well as medium thicknesses. Likewise, plasma cutting is more cost-effective for metals up to 10 mm thick. Plasma cutting is often used for sheets with larger dimensions and thicker sections. Water cutting is recommended for metals up to 460 mm thick or temperature sensitive metals.