Copper laser cutting
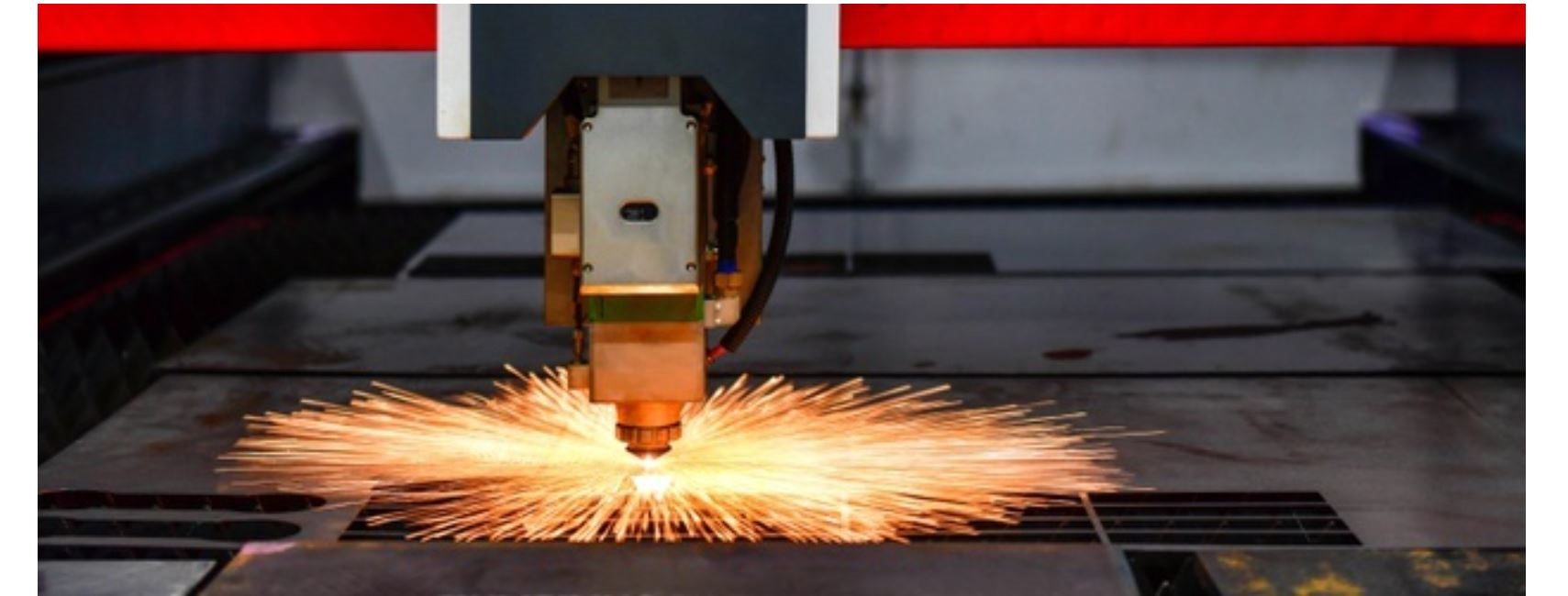
The use of laser cutting has several advantages, including the high flexibility of processing parameters and can also be used for complex geometries with different dimensions. This type of cut affects the surface in the form of thermal stress.
Copper laser cutting is used in engraving, kitchen utensils, shipbuilding, oil and gas industry, home applications and many other industrial applications. The use of laser cutting machines to cut metal parts with precision and quality, including copper cutting, has made the job easier for metal parts manufacturers. Laser cutting of copper is done in such a way that the excess parts of the metal sheet are burned, melted or evaporated. To keep the work clean, an engine is responsible for distributing the gas. In the laser cutting method of copper, a powerful light source directs to the desired surface and performs the cutting work. It should also be noted that the power of the device may vary depending on the material and thickness of the part.
Compared to traditional metal cutting methods, laser cutting of copper has greatly increased the accuracy of the work and is done more quickly, and it can be said that it is much more advanced and painless. In the traditional method, the metal was cut by creating high heat, which caused the metal to bend, but the use of copper laser cutting method reduces the bending ability of copper foil so that there was no need to fold after cutting. Copper cutting with laser devices is very quiet and has a high level of safety, which reduces the risk of working with this device to zero.
The advantages of laser cutting
Copper laser cutting has advantages such as: creativity in design, flexibility in complex designs, very high accuracy, high speed, low price, uniform accuracy in repetitive cutting, high quality and less waste. Also, mass cutting, simultaneous production of parts with the same thickness and elimination of several stages of the production process are other advantages of this type of cutting.
The maximum thickness of the laser cut is six mm, which can be changed up to 10% depending on the hardness of the metal. These machines are popular all over the world because of their non-mechanical, high cutting speed, high quality and cheap price. Another advantage of copper laser cutting is that it has the lowest losses and rotation compared to other methods. In repetitive cuts, the cutting work is done with the same accuracy and there is no limit in terms of geometric design. When cutting metal, it does not change the physical structure of the metal and also shows the standard smoothness after cutting the workpiece.
Important points of copper laser cutting
Cone angle: This involves changing the diameter of the hole in the thickness of the cut.
Folding production: The fewer folds after cutting, the better the final quality and the less the need for a second machining.
Crest: Crest actually determines the smallest cutting radius, which depends on the thickness of the sheet metal and is best considered in the project. For example, many corners have openings. In addition, the minimum number of holes that can be drilled in the sheet depends on the thickness of the sheet. Obviously, the shallower the machine, the more complex the lines and the finer the gears.
Cutting speed: Much depends on the capabilities of the machine and the power of the laser beam. The higher the power of the machine, the faster the cutting speed.
Surface smoothness: One of the most important parameters of cutting is smooth surface and no oxidation, which is created by combining different technologies and correct and accurate adjustment of control parameters such as gas type, gas pressure, cutting speed and laser.
Cutting copper metal is possible using a laser cutting machine, but it is not cost-effective for consumers to use this method. Copper has a poor ability to absorb infrared radiation due to its light-reflecting properties. In other words, copper is an excellent reflector for laser beams.
The reflection of these materials increases sharply when the metal is heated and decreases sharply when it melts. As a result, the reflection of the molten copper laser beam is less than 70%. This is because shiny metals such as copper absorb a significant amount of laser beam in the molten state.