برش هواگاز
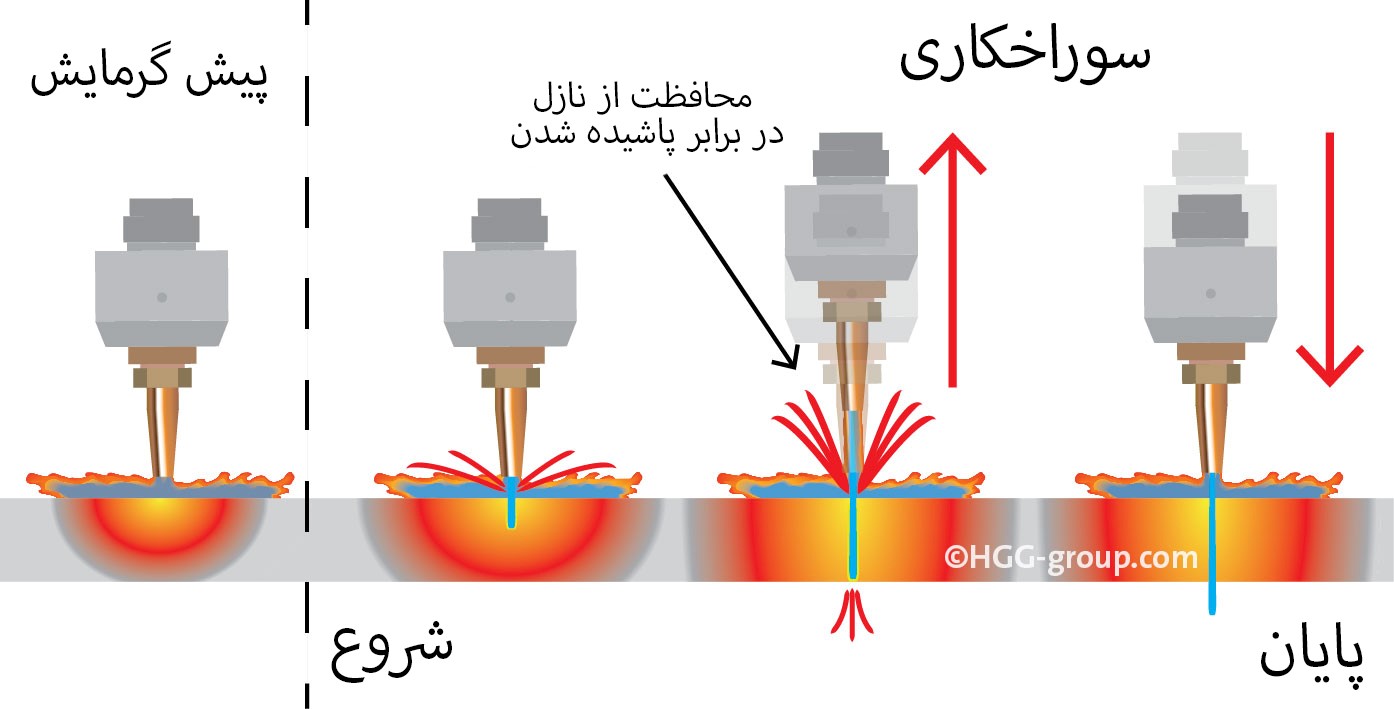
برش هواگاز یک روش برش قابل اعتماد، دقیق و رقابتی است که برای برش فولاد خفیف استفاده می شود. هنگام انجام اتوماتیک این فرایند برش، چه ویژگی هایی باید در نظر بگیرید؟ این ابزار مربوط به کیفیت کل کانتور اتصالات است تا زمان اتصالات و جوشکاری کاهش یابد.
اصول اولیه
قبل از برش، مشعل برش باید فولاد را از قبل گرم کند تا در نقطه شروع به احتراق برسد. در این دمای حدود 960 درجه سانتیگراد (بسته به نوع آلیاژ)، فولاد خاصیت محافظتی در برابر اکسیژن را از دست می دهد و هنوز جامد است. سپس اکسیژن خالص از طریق نازل به منطقه گرم شده هدایت می شود. این جریان اکسیژن ریز و فشار بالا با یک واکنش گرمازا، فولاد از قبل گرم شده و محافظت نشده را به فولاد مایع اکسید شده تبدیل می کند.
نقطه ذوب این فلز نیمه سوخته "سرباره" کمتر از فولاد است، بنابراین جریان اکسیژن می تواند سرباره مایع را بدون تأثیر بر فولاد جامد غیر اکسید شده، از حفره خارج کند. این واکنش گرمازا یک روند مداوم است و با حرکت مشعل برشی ایجاد می کند. برای ادامه کار واکنش گرمازا، مشعل برش، فولاد را در حین برش گرم نگه می دارد. تنها فلزاتی که نقطه ذوب اکسیدهای آنها کمتر از خود فلز پایه است می توانند با این فرآیند برش داده شوند. در غیر این صورت به محض اکسید شدن فلز، با تشکیل پوسته محافظ، اکسیداسیون را خاتمه می دهد. تنها فولاد ملایم و برخی از آلیاژهای ضعیف شرایط فوق را دارند و می توانند با فرآیند سوخت اکسیژن به طور موثر برش داده شوند.
کنترل سرعت و پیش گرم شدن
برش با هواگاز به خصوص برش مواد دارای دیواره ضخیم، یک فرایند زمانبر است. کمترین فاصله از طریق مواد یک برش عمود بر دیواره است. در صورت برش مورب (برش زاویه دار برای آماده سازی جوش) مشعل برش در یک زاویه قرار می گیرد و انتقال حرارت به مواد کمتر از برش عمود بر آن است و طول برش بیشتر خواهد بود. این امر برای حفظ برش دقیق زاویه دار به دستگاه تنظیم خودکار و کنترل سرعت نیاز دارد.
با استفاده از یک مشعل اضافی برش هواگاز که می توان عمود بر ماده نصب کرد، می تواند سرعت برش را به طور قابل توجهی بهبود ببخشد. (100 در زاویه برش 70 درجه و 50 در زاویه برش 45 درجه ). برای جلوگیری از مصرف غیرضروری گاز، این پیش گرم کن باید فقط برای زاویه های تندتر از 30 درجه فعال شود.
محافظت از پاشیده شدن نوک برش در هنگام سوراخ کردن
پیرسینگ نفوذ اولیه سطح مورد برش است و از همان فرآیند گرمازایی استفاده می کند که در هنگام برش استفاده می شود. پس از پیش گرم شدن سطح، اکسیژن از طریق نازل جریان می یابد تا فولاد از قبل گرم شده جامد را به فولاد اکسید شده مایع (فلز) تبدیل کند. پس از پیش گرم شدن سطح، اکسیژن از طریق نازل جریان می یابد تا فولاد از قبل گرم شده جامد را به فولاد اکسید شده مایع (سرباره) تبدیل کند. در طی این فرآیند پاشیدگی اتفاق می افتد، زیرا اکسیژن در هنگام سوراخ کردن، سرباره را به سمت بالا می برد. این پاشیده شدن می تواند به نوک برش بچسبد و بر جریان گاز و روند برش تأثیر بدی بگذارد. برای محافظت از نوک برش در هنگام پاشیده شدن، مشعل برش در هنگام سوراخ کردن به سمت بالا حرکت می کند و به محض سوراخ شدن مواد به فاصله صحیح تا ماده برمی گردد.
تغییر در این روش سوراخ کردن مشعل با قرار گرفتن در زیر یک زاویه کوچک تنها برای محافظت از نوک برش در برابر پاشیده شدن نیست بلکه برای محافظت از قسمت زیرین ماده برش در برابر پاشیده شدن (به عنوان مثال در داخل لوله) بکار برده می شود.
سوراخ کاری متناسب
هنگام برش مواد با دیواره ضخیم، تعیین زمان و درجه حرارت مناسب برای پیش گرم کردن، به طوری که حتی عمیق ترین قسمت مواد نیز تا دمای مناسب گرم شود، کار بسیار دشواری است. این کار به تمرین و تجربه زیادی نیاز دارد.
هنگامی که مواد غلیظ کمی بیش از حد طولانی از قبل گرم شوند، ورودی اکسیژن باعث پاشیده شدن زیاد و ایجاد یک دهانه بزرگ می شود. این به دلیل ضخامت دیواره و مقدار بیش از حد سرباره مایع است. از طرف دیگر، در صورت عدم استفاده از پیش گرمایش کافی، ضخامت کامل دیواره برای حفظ روند گرمازا به دمای اشتعال نخواهد رسید. این فرآیند در نیمه راه متوقف می شود و اپراتور باید در یک نقطه شروع دیگر، دوباره امتحان کند و آسیب به کانتور اتصالات نیاز به سنگ زنی و جوشکاری بیشتری دارد.
برای تنظیم خودکار این فرآیند می توان روشی به نام سوراخ کاری متناسب را اعمال کرد که به وسیله آن جریان اکسیژن تنظیم می شود تا فرایند گرمازایی در حین سوراخ کردن کنترل شود. پس از مدت کوتاهی از پیش گرم شدن برای رسیدن سطح مواد به دمای اشتعال، فرآیند سوراخ کردن با فشار اکسیژن کم شروع می شود. همانطور که مشعل به سمت نقطه اولیه کانتور نصب و برنامه ریزی شده حرکت می کند، به تدریج تغییر زاویه می یابد. در حالی که همزمان فشار اکسیژن به تدریج به حداکثر فشار افزایش می یابد تا روند گرمازا ادامه یابد و عمیق تر شود. شیب باعث ایجاد فضای لازم برای سرباره مایع می شود و همچنین باعث به حداقل رسیدن پاشیده شدن (محافظت از نوک برش) می شود.
آسیب سطح برش در شروع و پایان
شروع برش باید همیشه نزدیک به کانتور نصب شده و در یک منطقه به اصطلاح اوراق انجام شود تا از سوراخ شدن سطح برش جلوگیری شود. حرکت مشعل از منطقه اوراق به سمت موقعیت و زاویه شروع، ورودی نامیده می شود. حرکت مشعل به داخل اوراق پس از اتمام برش، خروجی نامیده می شود.
برای ایجاد یک ضربدری صاف و کنترل شده از ابتدا و انتهای برش (همان نقطه)، می توان مشعل را طوری برنامه ریزی کرد که در ابتدا به صورت شعاعی حرکت کند و سپس به بیرون شعاع برود.
ویژگی های برش هواگاز در مقایسه با پلاسما
• مواد و متریال
از برش هواگاز برای برش فولاد خفیف استفاده می شود. تنها فلزاتی که نقطه ذوب اکسیدهای آنها کمتر از خود فلز پایه است می توانند با این فرایند برش داده شوند. در غیر این صورت به محض اکسید شدن فلز، با تشکیل پوسته محافظ، اکسیداسیون را خاتمه می دهد. تنها فولاد ملایم و برخی از آلیاژها شرایط فوق را دارند.
• ضخامت دیواره
برش هواگاز امکان برش دیواره ضخیم و سپس پلاسما را فراهم می کند. پلاسما نمی تواند دیواره های ضخیم تری را برش دهد زیرا انرژی زیادی برای رسیدن به ضخامت های مشابه لازم است.
• زاویه برش
سوخت اکسی به دلیل غلظت پرتوی اکسیژن باعث کاهش زاویه های تندتر تا 70 درجه (در مقایسه با 45 درجه با پلاسما) می شود.
• برش های مستقیم
هنگامی که زاویه بیش از حد شیب دار باشد، پرتوی پلاسما تمایل به انحراف دارد. با این حال، این انحراف می تواند توسط دستگاه تنظیم خودکار جبران شود.
• هزینه
برش هواگاز یک راه حل مقرون به صرفه تر از برش پلاسما است. هزینه های اولیه آن شامل سرمایه، مواد مصرفی و هزینه های عملیاتی کمتر از برش پلاسما است. با این حال، سرعت پردازش معمولاً کمتر از محدوده ضخامت دیواره 20 میلی متر است (با در نظر گرفتن پروفیل های سه بعدی در صنعت فولاد سنگین).